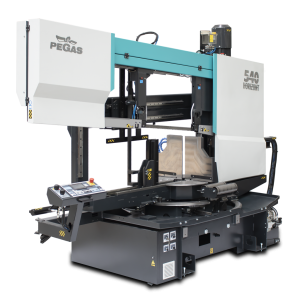
mm | 0° | 45° | 60° | -45° | -60° | ![]() |
![]() |
---|---|---|---|---|---|---|---|
![]() |
540 | 510 | 350 | 510 | 310 | 750x450 | x |
![]() |
75x490 | 510x490 | 350x490 | 510x490 | 310x490 | 750x450 |
![]() |
![]() |
![]() |
![]() |
![]() |
---|---|---|---|---|
3x400V | 5,5 | 15-150 | 6880x41x1,3 | 2370 |
Lmin | Lmax | Bmin | Bmax | Hmin | Hmax | V |
---|---|---|---|---|---|---|
3480 | 4696 | 1756 | 1756 | 2400 | 2510 | 810 |
- Highly productive, semi-automatic dual column band saw machine.
- The saw is designed for cutting material in both straight and angular cuts, angular cuts adjustable 150° left, 90° perpendicular, 30° right (+/- 60 degrees).
- The saw is designed for cutting bars of solid material and profiles.
- Saw is used in series production in industrial plants. The saw is designed for cutting straight bars of steel material.
Control system:
- The machine is equipped with programmable PLC MITSUBISHI FX5_U64. The saw blade drive and arm movement are completely controlled by MITSUBISHI technology.
- The colour touch screen allows easy communication with the machine operator. It shows working states such as blade speed, cutting feed and the status of individual working movements.
- Display size 4.3' (56x96mm)
- Control of the cutting feed is ensured by a hydraulic throttle valve with RTR function.
- RTO (rotate to) function for automatic rotation to set angle.
- The control panel is located on the console in a safe position. The control panel includes a digital display of the saw control system and a high quality foil keypad. The keypad is used to control the basic movements of the saw (movement of the arm, turntable and vice) and to start the saw's working cycle. The control panel is also equipped with a safety button to stop the saw.
- Safety module with self-diagnosis.
- 24V control
Construction:
- The saw is designed to fully support the efficient use of carbide saw blades. The band saw has a robust design to withstand extreme stresses in production conditions. All machine components are designed and optimized to minimize vibrations and allow maximum cutting performance of the machine.
- The saw arm with the columns close to the clamping vice and the saw blade close to the columns minimize vibrations and allow maximum cutting performance of the machine.
- Saw blade speed range 15 - 150m/min.
- The arm is a robust weldment and is designed to ensure the necessary rigidity and cutting accuracy
- The saw blade is driven by a bevel gearbox, asynchronous motor and frequency inverter.
- External fan cooling of the saw blade drive.
- The arm moves on two columns using a four-row linear guide with a high load capacity.
- Arm movement by hydraulic cylinder
- The saw blade is guided on robust cast iron pulleys.
- WRS - Reinforcement of pulley mounting - drive pulley mounted directly on the output shaft of the gearbox. The pulley is supported on both sides by a bearing seat =minimizing the load on the shaft seat. The tension pulley is held/tensioned by two hydraulic cylinders at both ends of the centre pin =significant reduction of stress and extension of the life of the bearing. The tension pulley mounting is with zero play=conical bearings secured by KM nut.
- The saw uses a sensor and magnetic tape to evaluate the position of the arm above the material. The upper and lower working position of the arm is set by entering a value into the saw control system. The lower end position can also be determined by a limit switch.
- Main vise with split clamp for fixing the workpiece before and after the cut (straight cuts). The clamps ensure secure clamping of the material.
- Movement of the clamp of the main vise in the rigid steel guide by means of a long-stroke hydraulic cylinder.
- Two robust vise support clamps
- Control valve for vise pressure adjustment, pressure indication on pressure gauge
- The turntable is a robust weldment. Rotary table for angle cuts with machined base guide surface. The rotary table adds a large space for supporting the material and clamping it precisely. Rotation of the angle cutting table by means of a hydraulic cylinder and a linear guide, driven by gear and rack.
- Angle adjustment control:
o Rotation via the button to the desired angle (fast-shift / slow-shift)
o Using the RTO (rotate to position) function with automatic adjustment of the desired arm rotation position
- Hydraulic position locking "lock"
- Turntable angle displayed on the Mitsubishi control panel display. Indication of set angle by incremental sensor and magnetic tape.
- Optimisation of the chip movement to the chip box or chip ejector, which is offered as an accessory
- Belt guidance in guides with plates and guide bearings and on cast iron pulleys. Adjustable guides with zero cutting clearance, preloaded by plate springs.
- Robust flange with drive shaft mounting via roller bearing.
- The inclination of the saw blade against the plane of the vise is 7 degrees. This ensures higher performance when cutting profiles and bundles and at the same time increases the life of the saw blade.
- The saw has a guide on the drive side mounted on a fixed beam. On the tensioning side, the guide is mounted on a sliding beam.
- Blade guide beam adjustable over the entire working range. The movement of the guide is linked to the movement of the vice clamp. It is therefore not necessary to manually adjust its position.
- The guide beam moves by means of a linear guide (2 rails, 3 trolleys) with high load capacity.
- A new way of mounting the guides - a solution with a regulated spacer.
- BGT-S - mechanical pressure of the saw blade in the guides by means of disc springs
- The space between the saw blade guide and the pulley is provided with a cover to protect the operator from the moving saw blade. The covers also protect the surrounding area from falling chips and cooling emulsion.
- The saw is equipped as standard with hydraulic saw blade tensioning - allowing ideal cutting conditions to be maintained at all times. The tensioning force is provided by 2 hydraulic cylinders.
- Automatic Indication of correct saw blade tension by means of a pressure sensor. Cleaning brush passively driven by a pulley in the basic version, electric motor as optional
- Cooling system for cutting emulsion, fed into the blade guides and directly into the cutting channel using the flexible LocLine system.
- Robust base with chip tray. The base is designed for handling the saw with a crane
- Microswitches for opening pulley covers.
- Hydraulic unit located outside the base - better cooling and access. The hydraulic unit controls the functions of the saw: movement of the arm, opening and closing the main vice, rotating the turntable for angle cuts and fixing the turntable in the set rotation. The hydraulic oil pump is located outside the oil tank.
- Two rollers for supporting the cut material. Retractable via linear guide. Positioning on the output side
- Cover bodywork that covers the movements of the rear of the arm. The body minimises the risk of injury and contamination of the saw's surroundings with chips and cutting emulsion.
- Chip rinsing pistol
- LED strip for work area lighting.
Basic equipment of the machine:
- Saw blade
- Tool set for routine machine maintenance.
- Operating instructions in electronic form on CD.
Code | Description | Type | |
---|---|---|---|
MITSUBISHI | Controling system MITSUBISHI. | ST | |
540-HMI+FK | HMI = colour control touch screen. FK=foil keyboard with basic movements | ST | |
ZAPSI | Industry 4.0, Connection to bandsaw monitoring and evaluation of machine efficiency, operation, production, and energy consumption. | OP | |
540-OPE | Control panel on a freestanding external console. | OP | |
F | Motor and frequency converter for a fluent change of the circumferential speed of the blade. | ST | |
540-DRIVE | Motor (5,5 kW) + bevel gearbox | ST | |
540-HM-DRIVE | More powerfull motor (7,5 kW) + bevel gearbox optimal for full use of the carbide (HM) saw blade. Calculated as assesories | OP | |
WRS | Reinforcement of wheel mounting. The tensioner wheel shaft is reinforced with an additional hydraulic cylinder, the drive wheel shaft is reinforced with a bearing and a beam mounted to the frame. | ST | |
NPH-2 | Hydraulic band tension with two hydraulic cylinders located on both sides of blade tension wheel. | ST | |
IRP | Down shift speed indication value on the display of control system ( mm/min ) | ST | |
RTR | Regulation press of arm. Cutting conditions optimalization (regulates force that push the blade to the material so this function increases blade lifespan). | ST | |
HPV | Solution of moving guides of band together with jaws of the vice. | ST | |
PCK | Cleaning brush of blade, driven passively (driven by pulley). | ST | |
540-H-ECK | Cleaning brush of blade driven actively by motor. D=125 mm. Belt drive, 790 RPM. | OP | |
LED | Lighting of workink space. | ST | |
540-PUH+PUD+RTO | PUH = Hydraulic turning of the turntable, including hydraulic position fixation. PUD = Angle indication-digital. Shows the set angle on the digital display. RTO = automatic rotation to set angle | ST | |
540-PVP | Supportin cylinder , situated on the base of the saw on the linear feeding - Inpout (left) side. | ST | |
540-PVZ | Supportin cylinder , situated on the base of the saw on the linear feeding - outpud (right) side. | ST | |
540-CLT | Automatic lubrication of the turntable movement by the modified MINI-LUBE systém | OP | |
540-CSE | Centre section of the turntable (cut-through segment). CSE = central segment. | OP | |
540-GPP | Support plate of the cut material before cutting. Only for cutting perpendicular cuts, mounted instead of the PVP support roller. | O | |
540-GPZ | Support plate for the cut material behind the cut. Only for cutting perpendicular cuts, mounted instead of the PVZ support roller. | O | |
RTS | Regulation press of vice. | ST | |
540-VTT | Universal pusher chip ejector without centre tube, included 1 Pc of BOX-TRI-L2 | OP | |
540-VTT-D | Optional chip conveyor extension for transportation of chips. Available only together with 540-VTT. | OP | |
540-H-LSG | Optical protection fence that protects the machine operator from dangerous movements of the saw components in the automatic cycle. | OP | |
540-H-LSG-Z | LSG-Z is an optical protective fence placed behind the saw. | OP | |
540-HP1 | Collision-free long-stroke top pressure. Located on the pivoting part of the saw. Movement of the jaw on 2 rails and 4 carriages of linear guideway. Transverse feed: loose fit on linear guide, manual position adjustment. **not applicable for CNC angle cutting | OP | |
540-HP2 | Collision-free long-stroke vertical clamp. Positioned on an attachment frame on the saw. Movement of the jaw on 2 rails and 4 carriages of linear guideway. Designed for cutting bundles, a saw fitted with this device can cut 45 deg. angled cuts with limited turntable rotation to the left only. Easy disassembly, transport by crane. | OP | |
SRZ-Z-800 | Additional vice mounted on the standard RDT roller conveyor. Long stroke jaw (stroke 800mm) operated by hydraulic cylinder. The jaw control is coupled to the jaw of the main saw vice. | OP | |
MINI LUBE 41 | Wasteless lubricating system – 2 pumps, for blade 41 mm. Instead of emulsion cooling, specially for cutting profiles and non-ferrous metals, necessary supply of pressed air 6 Atm. | O | |
LASER LINE | Laser indicator of cut position. | O | |
540-H-CKN | Nylon cleaning brush 125 mm | OP | |
540-H-SET M42 | Set of 10 blades in SPECTRA M42 quality – customer chooses blade's TPI. Blade specs: 6880x41x1,3 | O | |
540-SET M51 | Set of 10 blades in DURATEC M51 quality – customer chooses blade's TPI. Blade specs: 6880x41x1,3 | O | |
540-H-NAV | Instruction Manual – printed version. | O | |
PAL4 | Packing on the palette 1,5 m x 3,5 m. | O | |
VD-2000/800/89/6 | Input or output roller conveyor with a gutter which prevents leakage | O | |
VD-V-800 | Aditional cylinder, lenght 780 mm. | O | |
VD-BL | Support from vertical side - bearing. Assambled on VD1 | O | |
VD-VB-190 | Vertical cylinder 190 mm assamblen od the VD1. | O | |
540 RDL 1000 | Left side connecting roller conveyor. Provides connection of the saw with RDT, RDM. Length 1000 mm, width 620 mm, 5 rollers, load capacity 850 kg/m. Includes function of automatic shifting of 3 support rollers when the saw is angled. Placement of 3 rollers on linear guide. | O | |
540 RDR 1000 | Right side connecting roller conveyor. It provides connection of the saw with RDT, RDM. Length 1000 mm, width 620 mm, 5 rollers, load capacity 850 kg/m. Includes function of automatic shifting of 3 support rollers when the saw is angled. Placement of 3 rollers on linear guide. | O | |
540-RBR-RDR/L | Side roller with bracket for mounting on roller track RDR/RDL | O | |
RDT 1000/800 | Robust roller conveyor with coolant gutter. Length 1000 mm, width of cylinders 800 mm, 3 rollers, load capacity 2700 kg/m. | O | |
RDT 2000/800 | Robust roller conveyor with coolant gutter. Length 2000 mm, width of cylinders 800 mm, 5 rollers, load capacity 2700 kg/m. | O | |
RDM 2000/800 | Input or output robust motorised roller table. Powered by electric motor, worm gearbox and inverter. Width 800 mm, length 2000 mm. Load capacity 2700 kg/m. For automatic CNC saws can only be used with SYNC-2 accessories | OP | |
RDML 2000/800 | Input or output robust roller conveyor with driven rollers. Driving from RDM throught chain. (RDM-L does not work without RDM conveyor). Width of cylinders 800 mm, length 2000 mm. Load capacity 2700 kg/m. | OP | |
VZM-800 | Hydraulic operated lifting motorized cylinder, width 800 mm. VZM is designed to lift the material using hydraulic short-stroke cylinder above the level of other rollers on the conveyor. After lifting the VZM can move the material forwards or backwards by electric motor. VZM is installed instead of 2 original passive cylinders. VZM is operated independently with own control panel. VZM works only with RDT 2000. | OP | |
500x750-RBR | Side support fixed cylinder, height 280 mm, diameter 92 mm with its own frame, mounted to roller tables RDT. | O | |
500x750-RBRS | Side adjustable roller with its own steel frame, and with the movable leading 800 mm, fixed by 2 pcs of T-nuts. Height 280 mm, diameter 92 mm. | O | |
RDH-800 | Independent movable cylinder, adjustable height, capacity 700 kg.Width of roller 800mm. | O | |
V-800 | Additional roller placed between rollers of RDT table. Price for 1 pc. Impossible to install on VD roller conveyors. | O | |
RDT-XY1-800 | Roller table setup (with one motorised VZM-800). The setup has total Length 7500 mm. In this option is included 4 powered cross-conveyors with Length of 4000 mm. The flow of material is one way, manual control. Max. weight of material transferred per one segment: 1000 kg.For connection to the saw it is necessary to order RDR / RDL | OP | |
LMP 1000 | Measuring stop for defining the length of the cut bar. Fixed contact with the material to be measured. Length reading with scale measuring tape. | O | |
LMP 2000 | *Recommended for measuring lengths up to 2000mm. | O | |
LMP 3000 | * Recommended for measuring lengths up to 3000mm. | O | |
LMP 4000 | *Recommended for measuring lengths up to 4000mm. | O | |
LMP 5000 | *Recommended for measuring lengths up to 5000mm. | O | |
LMP 6000 | *Recommended for measuring lengths up to 6000mm. | O | |
LMPD 1000 | Measuring stop for defining the length of the cut bar. Fixed contact with the measured material. The length is shown on the display. | O | |
LMPD 2000 | *Recommended for measuring lengths up to 2000mm. | O | |
LMPD 3000 | * Recommended for measuring lengths up to 3000mm. | O | |
LMPD 4000 | *Recommended for measuring lengths up to 4000mm. | O | |
LMPD 5000 | *Recommended for measuring lengths up to 5000mm. | O | |
LMPD 6000 | *Recommended for measuring lengths up to 6000mm. | O | |
LMS 1000 | Measuring stop for defining the length of the cut bar. Sliding soft-contact with the material to be measured. Length reading with scale measuring tape. | O | |
LMS 2000 | *Recommend to use for measuring lengths up to 2000mm. | O | |
LMS 3000 | *Recommend to use for measuring lengths up to 3000mm. | O | |
LMS 4000 | *Recommend to use for measuring lengths up to 4000mm. | O | |
LMS 5000 | *Recommend to use for measuring lengths up to 5000mm. | O | |
LMS 6000 | *Recommend to use for measuring lengths up to 6000mm. | O | |
LMSD 1000 | Measuring stop for defining the length of the cut bar. Sliding soft-contact with the material to be measured.The length is shown on the display. | O | |
LMSD 2000 | *Recommend to use for measuring lengths up to 2000mm. | O | |
LMSD 3000 | *Recommend to use for measuring lengths up to 3000mm. | O | |
LMSD 4000 | *Recommend to use for measuring lengths up to 4000mm. | O | |
LMSD 5000 | *Recommend to use for measuring lengths up to 5000mm. | O | |
LMSD 6000 | *Recommend to use for measuring lengths up to 6000mm. | O |
Tech. data NO241 are valid on 1.1.2024. Producer has the right to make changes of technical data.
Values contained on this page are only for information purposes. This information is not an offer and is not a public promise. This indicative offer does not give right to close a contract. The only guiding document for the contract is a valid price list.
or send inquiry!