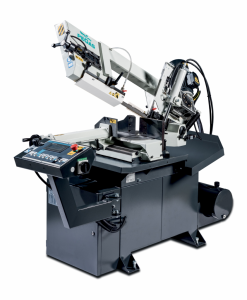
mm | 0° | 45° | 60° | -45° | -60° | ![]() |
![]() |
---|---|---|---|---|---|---|---|
![]() |
230 | 190 | 120 | 185 | x | x | x |
![]() |
280x220 | 180x170 | 120x90 | 180x120 | x | 280x120 | 230x120 |
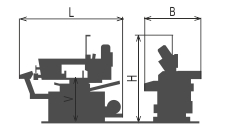
![]() |
![]() |
![]() |
![]() |
![]() |
---|---|---|---|---|
3x400V | 1,5 | 20-100 | 2720x27x0,9 | 420 |
Lmin | Lmax | Bmin | Bmax | Hmin | Hmax | V |
---|---|---|---|---|---|---|
1830 | 1950 | 890 | 1040 | 1370 | 1910 | 790 |
- Semiautomatic machine with hydraulic manipulation.
- The machine is designed for cutting of material in vertical and angle cuts, angle cuts are possible to set fluently from 60° right to 45° left.
- It is suitable for piece production and small series production.
- Thanks to its robust construction it enables cutting of wide range of materials including stainless steels and tools steels as well as profiles and full materials.
Control system:
- The Controler with PLC MITSUBISHI and features an automatic feed control BRP.
- Control panel MITSUBISHI as standard equipment. It uses touch display and PLC, which enable semi-automatic cutting (basic setting encluded) as well as communication with operator.
- Controler show lot of information about cutting proces on the display:
- Cutting cycle indication,
- indication BRP,
- indication – blade tightening,
- time of the cut,
- loading of blade in amperes,
- speed of the blade,
- cutting times measuring,
- list of error messages.
- User´s setting:
- autostop of hydraulic unit
- mode of arm moving after end of the cut
- mode fadt moving of the arm
- mode time lag of shift speed
- mode blade moving
- mode jaw moving after cutting cycle finish
- diagnostic of inputs and outputs
- STOP function – cutting: it enables to stop cutting by pressing STOP button at any time. The Frame goes up with the running blade without opening the vice.
- Regulation of shaft speed (moving to cut) is manual and uses throttle valve placed beside control panel. Automatic (safety) regulation of shift speed PEGAS BRP. Principle: Machine will stop after exceeding set loading (defined in ampers).
- The ergonomical control panel is mounted on the movable console. The control panel is equiped with mechanical buttons and digital display of the machine control system. Mechanical buttons controls basic saw movements (arm, vice) and cutting cycle start. The safety button is present on the panel aswell. Buttons for controlling the movements of the machine are part of a high-quality foil keyboard.
Construction:
- The machine is constructionaly designed in that way, so that it corresponds to standard exertions in productive conditions. That is why all carrying parts are made as cast-iron castings (solidity, absorbtion of vibrations and stops). Parts of arm, vice and turn table is cust iron.
- The arm of the machine is made of cust iron and it is designed to ensure the power and the precision of the cut. Arm is 25 grades sloped, it increases the lifetime of
- The arm rotated by a shaft (joint) which is support by adjustableconical bearings
- Drive pulley and tighten pulley are both metal castings.
- Upper working arm position controled by automatic stopper (DPP)
- The down working position of the arm controlled by the miscroswitch. In the end position microswitch is on, arm goes to selected upper position.
- The vice is made from cast iron. Jaws ensure safe clamping of the material.
- The hydraulically operating vice with short travel is placed in an adjustable dovetail groove.
- Moving jaw of the vice is manual with a wheel and trapeze thread.
- Basic part of the vice moves according to the direction of the angle cut setting, fixation is made by the handle.
- Turn table is cust iron. A turntable gives a big place for supportion of material and its perfect clamping.
- Manuall turning of the table for angle cuts, angle fixation using quick clamping lever.
- General angles are adjusted by the nonius.
Basic equipment of machine:
- The blade leading in guides with hardmetal plates and leading bearings and along cast iron pulleys.
- There is a guide situated on the firm beam on the drive side. On the tightening side there is the guide situated on the moving beam.
- The guide beams of moving band guide is adjustable in whole working range. Manual adjustment and fixing of the guide beams.
- The saw-band is equipped with a guard, which protects the operator from millings and cutting emulsion.
- Mechanic tightening of the blade.
- Automatic indication of blade tension.
- A passive driven cleaning brush for perfect cleaning and function of blade.
- Drive of machine is solved by worm gear box with maintenanceless oil filling. Three-phases electromotor with double winding, with a frequency converter for a fluent regulation of the blade speed from 20 to 100 m/min. Sturdy flange with shaft. Termoprotection of engine.
- The cooling system distributes cutting emulsion to the band guides.
- Massive base with a tank for chips. Base is designed for manipulation manipulation with machine by pallet truck and also by any hight lift truck.
- Indication of blade tightening and opening of the cover.
- Controlling 24 V.
- Maschine is equipped with hydraulic system which controles all functions of that maschine. It pushes the arm to cut, pulls up the arm and opens and closes vices.
Basic accessories of machine:
- Measuring end stop.
- Band saw blade.
- Set of spanners for common service.
- Manual instructions in eletronic form (CD).
Operating cycle:
After manual adjustment of the jaws the operator starts the cycle with a switch on the control panel. The hydraulic cylinder of the vice grips the material and the saw starts working. The cutting speed of the arm is controlled by a throttle valve. Arm and vice movements after cut finish following set user parameter. The vice opens and the operator can handle the material.
Code | Description | Type | |
---|---|---|---|
MITSUBISHI HMI 4,5" | Control system MITSUBISHI with display 4,5“ | ST | |
ZAPSI | Industry 4.0, Connection to bandsaw monitoring and evaluation of machine efficiency, operation, production, and energy consumption. | OP | |
F | Motor and frequency converter for a fluent change of the circumferential speed of the blade. | ST | |
DPP | Mechanical workstop for upper frame position. | ST | |
230-OZM | Measuring end stop which is mounted directly to the machine, length 1m. | ST | |
240-CK | Cleaning brush of blade, driven passively (driven by sawing blade). | ST | |
PEGAS-BRP | Electronical regulation of the down-shift. | ST | |
230-HP | Hydraulical upper vice. Hydraulic upper clamping tighten the material in vertical sense by the hydraulic cylinder. | OP | |
BOX-PCS | Box for cutted pieces with emulsion draining to the waterproof tank. | O | |
BOX-TRI | Box for the chips with emulsion draining to the waterproof tank. | O | |
BOX-TAH | Tool for manipulation with BOX-PCS and BOX-TRI. | O | |
MINI LUBE 27-34 | Wasteless lubricating system, instead of emulsion cooling, specially for cutting profiles and non-ferrous metals, necessary supply of pressed air 6 Atm. | O | |
LASER LINE | Laser indicator of cut position. | O | |
LIGHT L1 | Lighting of working space. | OP | |
230-SET M42 | Set of 10 blades in M42 quality – with customer’s choice of teeth. 2720x27x0,9 | O | |
230-SET M51 | Set of 10 blades in M51 quality – with customer’s choice of teeth. 2720x27x0,9 | O | |
WGUN1 | Spray gun for rinsing chips is used for a quick and easy cleaning of the machine from chips and burrs. | O | |
230 - NAV | Manual instruction – printed version. | O | |
PAL EUR | Packing on the palette 0,8 m x1,2 m. | O | |
OBAL1 | Package - wooden box 1,2 m x 2,0 m. | O | |
OBAL-230 | Packing in the wooden cage. | O | |
230 RDZ | Output connecting part of the roller conveyor RD - ensures angle cuts of the machine, length 1000 mm, width 290 mm, bearing capacity 200 kg/m, adjustable leg includedd in price. | O | |
230 RDP | Input connecting part of the roller conveyor RD-ensures angle cuts of the machine, length 1000 mm, width 290 mm, bearing capacity 200 kg/m, adjustable leg includedd in price | O | |
RD 1000/290 | Roller table. Length 1000 mm, width of cylinders 290 mm, capacity 200 kg/m, adjustable | O | |
RD 2000/290 | Roller table. Length 2000 mm, width of cylinders 290 mm, capacity 200 kg/m, adjustable | O | |
RB 200 | Side vertical fix cylinder, height 200 mm, monted on the RD tables | O | |
RD VR-290 | Robust cylinder length 290 mm with the bearing for RD roller coneyor. The capacity of roller table increased from 200 kg/m to 400 kg/m | O | |
RBS 200/290 | Side vertical movable cylinder, height 200 mm, working only with RB. | O | |
RHS 290 | Horizontal cylinder , working only together with RB + RBS for bundle fixing, length of cylinder 290 mm | O | |
RDN | Support for RD. | O | |
R290 | Movable cylinder, adjustable height, width 290 mm, capacity 200 kg. | O | |
OZ 0000 | Second movable stop for OZ. | O | |
OZ 1000 | Mechanic measuring system with the meter L = 1200 mm. | O | |
OZ 2000 | Mechanic measuring system with the meter L = 2200 mm. | O | |
OZ 3000 | Mechanic measuring system with the meter L = 3200 mm. | O | |
OZ 4000 | Mechanic measuring system with the meter L = 4200 mm. | O | |
OZ 5000 | Mechanic measuring system with the meter L = 5200 mm. | O | |
OZ 6000 | Mechanic measuring system with the meter L = 6200 mm. | O | |
OZD 1000 | Mechanic measuring system with digital display 1 meter long. | O | |
OZD 2000 | Mechanic measuring system with digital display 2 meter long. | O | |
OZD 3000 | Mechanic measuring system with digital display 3 meter long. | O | |
OZD 4000 | Mechanic measuring system with digital display 4 meter long. | O | |
OZD 5000 | Mechanic measuring system with digital display 5 meter long. | O | |
OZD 6000 | Mechanic measuring system with digital display 6 meter long. | O |
Tech. data NO241 are valid on 1.1.2024. Producer has the right to make changes of technical data.
Values contained on this page are only for information purposes. This information is not an offer and is not a public promise. This indicative offer does not give right to close a contract. The only guiding document for the contract is a valid price list.
or send inquiry!