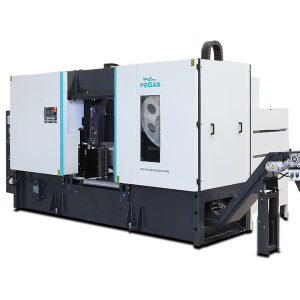
mm | 0° | 45° | 60° | -45° | -60° | ![]() |
![]() |
---|---|---|---|---|---|---|---|
![]() |
700 | x | x | x | x | x | x |
![]() |
750x700 | x | x | x | x | 750x460 | 750x700 |
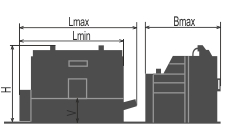
![]() |
![]() |
![]() |
![]() |
![]() |
---|---|---|---|---|
3x400V | 11,0 | 15-80 | 7680x67x1,6 | 10000 |
Lmin | Lmax | Bmin | Bmax | Hmin | Hmax | V |
---|---|---|---|---|---|---|
4350 | 5700 | 2010 | 2500 | 2800 | 2800 | 615 |
- It is a highly efficient automatic hydraulically controlled band-saw with multiple material feed.
- The machine is designed for vertical
- It is suitable for serial production in industrial premises. The machine is designed to saw steel materials, but also non-ferrous and light metals. However, we recommend consulting the manufacturer about this option.
- No other materials may be sawn without approval from the manufacturer.
Control system:
- Machine is equiped with programmable PLC SIEMENS SIMATIC S7-1200. Drive of band blade, movement of arm and movement of feeder are completely controlled and drive by SIEMENS technology.
- The coloured touch screen HMI SIEMENS TP 700 COMFORT enables easy communication with an operator. It shows working conditions (blade speed, moving to the cut, cutting parameters etc.)
- The machine enables to work with two modes:
- SEMIAUTOMATIC CYCLE: The machine cuts the material immediatelly in a semiautomatic mode. The operator uses the feeder of the machine for the manipulation with the material and for the exact feed of the material into the cutting zone. The movement of the feeder is realized by manual buttons or by GTO function. After starting GTO function the operator sets the position of the feeder, presses START GTO button and feeder goes to the set position.
- AUTOMATIC CYCLE: the feeder feeds the material according to the set programm. The operator sets the cutting programm, machine realizes these programms, it is possible to make thousand different programms.The part of one programm is a complete setting of the cut: blade speed, feed speed, setting of an automatic regulation, setting of the hight of the bar to be cut, setting of the lenght of the bar, angles values and number of pieces. The lenght and number of pieces it is possible to set in 20 lines, the machine feeds differently set lenghts automatically.
- Regulation of cutting feed is realized by controlled system by the servo-motor and throttle valve of hydraulic. Then is reached very precise cutting feed. Operator will input into program requiered cutting feed (mm/min) and bandsaw this cutting feed precisely set.
- Two basic regimes of automatic system regulation (ASR): ARP a RZP.
- RZP = Zone regulation. System enable to cut material in 5 zones, because of setting optional cutting feed and blade speed according on blade position.
- ARP = System of the automatic regulation of the cutting feed rate depending on the cutting resistance of the material or blunting the blade. Systém offers two basic modes of ARP: BIMETAL and CARBIDE.
- BIMETAL mode is suitable for optimalization of the cutting feed when cutting profiles by bimetal blades. The cutting feed is higher if the blade cuts sides of the profile. As the blade reaches the full material, the system reduces the cutting feed automatically so that teeth gap of the blade would not be filled.
- CARBIDE mode is suitable for cutting of full bars. If the blade is old (blunt), loaded is the cutting feed reduced Reaction time is slower than in mode BIMETAL.
- The control panel is placed in the tightening pulley cover. The control panel is equiped with mechanical buttons and digital display of the machine control system. Mechanical buttons controls basic saw movements (arm, vice, feeder) and cutting cycle start. The safety button is present on the panel aswell. Buttons for controlling the movements of the machine are part of a high-quality foil keyboard.
- Safety module with autodiagnostics.
Construction:
- The machine is constructionaly designed in that way, so that it corresponds to extreme exertions in productive conditions. Massive construction enables using of carbid blades comfortably.
- The arm of machine with columns situated as near the clamping vice as possible minimizes vibrations and enables max. cutting performance.
- The arm of the machine is robust, heavy weldment and it is designed so that a toughtness and a precision of cut was ensured.
- The arm moves along two columns using a four row linear leading with a high loading capacity. Arm movement using two hydraulic cylinders.
- The robust steel pulleys sloped of 25 degrees regarding the level of the cut. Thanks to sloped arm the twist of the blade is eliminated and these is possibility to bring the blade closer to the minimal distance from the linear leading on columns. This arrangement eliminates vibrations and enables the max. cutting performance of the machine.
- The arm uses incremental sensor for evaluation of current position above material. Upper working position of the arm is possible to set in control system.
- Down working position is set with adjustable mechanical stop and microswitch. Down working position of the arm is also possible to set in the saw control system. After reaching bottom working position the arm stops in the position set in the system.
- Vice is robust steel weldments.
- Main vice with divided jaw that clamps the material in front of as well as behind the cut. The jaws allow a safe grip.The optimalization of the chip movement through the fixed jaw directly to the chip extractor.
- Jaws move on two rails of linear leading using hydraulic cylinder. One jaw is longstroke (the movement by longstroke hydraulic cylinder), one is shortstroke (it releases its position when feeding the bar, the jaw is not worn out, the material does not slip). Shortroke jaw of he feeder and main vice with the short stroke rebound, it means contactless feeding of the crooked material.
- Regulation valves for setting a vice pressure in hydraulic system.
- Very rigid feeder with the feeding step 700 mm moves on four rails of the linear leading by hydraulic cylinders.
- There are two speeds of the feeder (micro feed when approaching the position). Periodic mode (feeder moves between zero position and the position of the set lenght of feed) or consecutive mode (feeder moves to the limit position, clamps the material and feed it to the cut consecutively.
- Incrementally straight sensor for indication of the position of the feeder and GTO (go to position) function. Feeder can have multiple feeding possibility.
- Indication of material in the feeder: optic sensor - it notices that there is a material in the feeder. If there is no material in the feeder, the signal reflects on the glass that is situated on movable jaw and it goes back to the sensor. The machine stops feeding and waits for another bar.
- The roller conveyer goes through the whole machine and supports the material in all its length. The roller conveyer of the feeder: bearings houses of the rollers are mounted into the basement – big robustness and precision.
- The feeder clamping vice is a robust steel weldment. Jaws ensure safe clamping of the material.
- Jaws of the feeding vice move along two-rails linears using hydric cylinder. One jaw is long stroke ( the movement by longstroke hydraulic cylinder). Second jaw is short stroke (utilization during bar feeding: not jaw wearing out, not slipping of material). Short stroke jaw is suitable for feeding of deformed material.
- Cutting zone is opened from side of the feeder device automatically, extends the blade lifetime when arm is moving to top position.
- The blade leading in guides with hardmetal plates and leading bearings and along cast iron pulleys.
- Machine is equipped with hydraulic system which controles all functions of that maschine. It pushes the arm to cut, pulls up the arm, opens and closes vices, moving of feeder.
- Blade leading though the guides solved by “clearanceless blade leading” – blade is push to guide by hydraulic clinder, which enables comfortable blade exchange
- There is a guide situated on the firm beam on the drive side. On the tightening side there is the guide situated on the moving beam.
- The guide beams of the blade are adjustable in the whole working range. A giude moving is connected with a vice-jaw movement so that to achieve the minimum distance of the guide and material. That is why it is not neccessary to set the position manually.
- The guide beam of the blade is placed in linear rails (2 linear rails and 4 bearings) with high bearing capacity.
- Hydraulic tightening of band.
- Automatic indication of blade tension.
- A cleaning brush is driven by an electroengine and ensures perfect cleaning of a blade.
- There is a planet gearbox and three-phase electric-motor with frequency inverter for fluent speed change in range of 20-100m/min.
- The cooling system for emulsion, leaded to the guides of the blade and by LocLine system directly to the cut groove.
- Massive base with a tank for chips and with chip extractors. Base is designed for manipulation manipulation with machine by crane.
- Indication of blade tightening and opening of the cover.
- Controlling 24 V.
Basic equipment of machine:
- Chip extractor
- Lighting of workink space.
- Band saw blade.
- Set of spanners for common service.
- Manual instructions in eletronic form (CD).
Code | Description | Type | |
---|---|---|---|
SIEMENS HMI 7" | Controling system SIEMENS with display 7". | ST | |
CDC | Basic library with cutting parameters, operator inputs the material informations (dimensions, type, quality) Automatical setting of cutting parameters. Operator set only information about quality and dimension of material. | ST | |
PCP | One year subscription for external machine programming (for Siemens control system) using www server. | O | |
BLUEBOX | Router for remote saw service. | OP | |
ZAPSI | Industry 4.0, Connection to bandsaw monitoring and evaluation of machine efficiency, operation, production, and energy consumption. | OP | |
LED | Lighting of workink space. | ST | |
DPP | Mechanical workstop for upper frame position. | ST | |
NPH | Hydraulic tension of band. | ST | |
HPV | Solution of moving guides of band together with jaws of the vice. | ST | |
PEGAS ASR | ASR = Automatic cutting feed regulation based on set parameters. | ST | |
RTS-A | Regulation press of vice – set of 2 pcs for bothvices. | ST | |
ECK | Cleaning brush of blade driven actively by motor. | ST | |
700-VTH | Chain chip extractor, includedd 1 pcs of BOX-TRI. | ST | |
CMU-1 | Opening of cutting zone from feeder side. Without contact moving of blade to upper position. | ST | |
OCP | Rebounding jaw of feeder vice. Controled by short-stroke cylinder, placed on linear leading. | ST | |
OCS | Rebounding jaw of stationary vice. Controls by short-stroke cylinder, placed on linear leading. | ST | |
BGT | Hydraulic clamping of the blade in the budie. Blade leading though the guides solved by “clearanceless blade leading” – blade is push to guide by hydraulic clinder, which enables comfortable blade exchange | ST | |
BOX-TRI-BIG | Box for the chips 200 l with emulsion draining to the waterproof tank. | O | |
700-HPR-A | Hydraulic upper clamping. Jaw clamps material in vertical direction using hydraulic cylinder and two axis of linear leading. Set of 2 pcs. | OP | |
MINI LUBE 67 | Wasteless lubricating system – 2 pumps, for blade 67 mm. Instead of emulsion cooling, specially for cutting profiles and non-ferrous metals, necessary supply of pressed air 6 Atm. | O | |
LASER LINE | Laser indicator of cut position. | O | |
700-ATB | Automatic feed of the material precisely into the cutting zone. | OP | |
700-ABP | Automatic, contactless setting of working position. | OP | |
700-KKR | Check of cut perpendicularity. | OP | |
700-GPZ 500 | Support table on the output side of the machine. Length 500mm. Horizontal stainless steel surface. Movement of cutting emulsion back into the machine, Connection with roller conveyors RDT / RDM. | O | |
700-SET M42 | Set of 10 blades in M42 quality – with customer’s choice of teeth. 7680x67x1,6 | O | |
700-SET M51 | Set of 10 blades in M51 quality – with customer’s choice of teeth. 7680x67x1,6 | O | |
700-NAV | Manual instruction – printed version. | O | |
700-RDT 1000/800 | Input or output robustroller conveyor with a gutter which prevents leakage of emulsion on the floor, width of cylinders 800 mm, length 1000 mm, capacity 2000kg/m. | O | |
700-RDT 2000/800 | Input or output robust roller conveyor with a gutter which prevents leakage of emulsion on the floor, width of cylinders 800 mm, length 2000 mm, capacity 2000kg/m. | O | |
SYNC-1 | Synchronisation of the saw feeder movement with the roller rotation of the RDM powered conveyor in the automatic cycle | OP | |
700-RDM 2000/800 | Input or output robust motorised roller table. Powered by electric motor, worm gearbox and inverter. Width 800 mm, length 2000 mm. Load capacity 2000 kg/m. For automatic CNC saws can only be used with SYNC-1 accessories | OP | |
700-RDML 2000/800 | Input or output robust roller conveyor with driven rollers. Driving from RDM throught chain. (RDM-L does not work without RDM conveyor) Width of cylinders 800 mm, length 2000 mm. Load capacity 2000 kg/m. | OP | |
700-RBR_530 | Side support fixed cylinder, height 530 mm, diameter 130 mm comes with its own frame, mounted to roller tables. It is possible to install only one RBR per roller conveyor. | O | |
700-RBR_400 | Side support fixed cylinder, height 400 mm, diameter 130 mm comes with its own frame, mounted to roller tables. It is possible to install only one RBR per roller conveyor. | O | |
700-RBRS | Side adjustable roller with its own steel frame, and with the movable leading, fixed by 2 pcs of T-nuts. height 650 mm. | O | |
700 V | Roller of roller table RDT put into gap. | O | |
700 V-P | Cylinder - full material. Price for one piece. | O | |
700 DMV 1000 | Cover of roller table, length 1000 mm. | O | |
700-TDT 2000/800 | Input or output extra robust roller conveyor, roller width 800 mm, length 2000 mm, 8 rollers. Load capacity 7000 kg/m. Comes with one vertical roller RBR. Cylinders are made from solid bars. | O |
Tech. data NO241 are valid on 1.1.2024. Producer has the right to make changes of technical data.
Values contained on this page are only for information purposes. This information is not an offer and is not a public promise. This indicative offer does not give right to close a contract. The only guiding document for the contract is a valid price list.
or send inquiry!