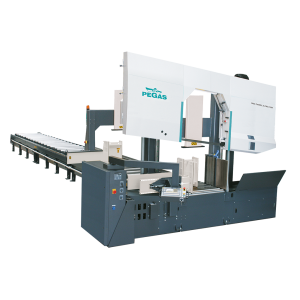
mm | 0° | 45° | 60° | -45° | -60° | ![]() |
![]() |
---|---|---|---|---|---|---|---|
![]() |
1000 | x | x | x | x | x | |
![]() |
1000x960 | x | x | x | x | 1000x650 |
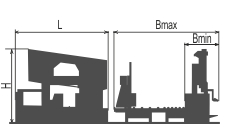
![]() |
![]() |
![]() |
![]() |
![]() |
---|---|---|---|---|
3x400V | 7,5 | 20-100 | 8920x54x1,6 | 9500 |
Lmin | Lmax | Bmin | Bmax | Hmin | Hmax | V |
---|---|---|---|---|---|---|
5050 | 5050 | 7200 | 7200 | 2960 | 3700 | 815 |
- Automatic two column band saw machine with complete hydraulic control.
- The machine is designed for vertical cuts.
- An unique construction of the band saw machine with three pulleys for leading of the blade.
- With the blade that is 8 grades sloped against the level guarantee high-efficiency of cutting.
- Highly efficient machine for cutting of construction steel of profile type. Secondary can be used for hardened material cutting.
Control system:
- Machine is equiped with programmable PLC SiEMENS SIMATIC S7-1200. Drive of band blade, movement of arm and movement of feeder are completely controlled and drive by SIEMENS technology.
- The coloured touch screen HMI SIEMENS TP 700 COMFORT enables easy communication with an operator. It shows working conditions (blade speed, moving to the cut, cutting parameters etc.)
- The machine enables to work with two modes:
- SEMIAUTOMATIC CYCLE: The machine cuts the material immediatelly in a semiautomatic mode. The operator uses the feeder of the machine for the manipulation with the material and for the exact feed of the material into the cutting zone. The movement of the feeder is realized by manual buttons or by GTO function. After starting GTO function the operator sets the position of the feeder, presses START GTO button and feeder goes to the set position.
- AUTOMATIC CYCLE: the feeder feeds the material according to the set programm. The operator sets the cutting programm, machine realizes these programms, it is possible to make thousand different programms.The part of one programm is a complete setting of the cut: blade speed, feed speed, setting of an automatic regulation, setting of the hight of the bar to be cut, setting of the lenght of the bar, angles values and number of pieces. The lenght and number of pieces it is possible to set in 20 lines, the machine feeds differently set lenghts automatically.
- Regulation of cutting feed is realized by controlled system by the servo-motor and throttle valve of hydraulic. Then is reached very precise cutting feed. Operator will input into program requiered cutting feed (mm/min) and bandsaw this cutting feed precisely set.
- Two basic regimes of automatic system regulation (ASR): ARP a RZP.
- RZP = Zone regulation. System enable to cut material in 5 zones, because of setting optional cutting feed and blade speed according on blade position.
- ARP = System of the automatic regulation of the cutting feed rate depending on the cutting resistance of the material or blunting the blade. Systém offers two basic modes of ARP: BIMETAL and CARBIDE.
- BIMETAL mode is suitable for optimalization of the cutting feed when cutting profiles by bimetal blades. The cutting feed is higher if the blade cuts sides of the profile. As the blade reaches the full material, the system reduces the cutting feed automatically so that teeth gap of the blade would not be filled.
- CARBIDE mode is suitable for cutting of full bars. If the blade is old (blunt), loaded is the cutting feed reduced Reaction time is slower than in mode BIMETAL.
The control panel is equiped with mechanical buttons and digital display of the machine control system. Mechanical buttons controls basic saw movements (arm, vice, feeder) and cutting cycle start. The safety button is present on the panel aswell. Buttons for controlling the movements of the machine are part of a high-quality foil keyboard. Safety module with autodiagnostics.
Construction:
- The machine is constructionaly designed in that way, so that it corresponds to extreme exertions in productive conditions.
- The arm of machine with columns situated as near the clamping vice as possible minimizes vibrations and enables max. cutting performance.
- The arm of the machine is robust, heavy weldment and it is designed so that a toughtness and a precision of cut was ensured.
- The arm moves along two columns using a four row linear leading with a high loading capacity. Arm movement using two hydraulic cylinders.
- 3 pulleys from cast iron are used.
- The arm uses incremental sensor for evaluation of current position above material. Upper working position of the arm is possible to set in control system.
- Down working position is set with adjustable mechanical stop and microswitch. Down working position of the arm is also possible to set in the saw control system. After reaching bottom working position the arm stops in the position set in the system.
- Main vice is massive steel weldment. Its jaws are iron casting.
- Hydraulic, long stroke main vice. Jaws enable well clamping of material.
- Jaws of the main vice move on two rails of linear leading using hydraulic cylinder. One jaw is longstroke (the movement by longstroke hydraulic cylinder), one is fixed.
- Regulation valves for setting a vice pressure in hydraulic system.
- Very firm feede is moving along 4-rails linears. The feeder movement is provided by bevel gear box, cogwheel and geared rack.
- Transporter is driven by electric engine with mechanical brake and frequency convertor.
- Indication of actual position by incremental sensor, which reads operating speed of gearbox output shaft.
- Indication of material in the feeder: optic sensor - it notices that there is a material in the feeder. If there is no material in the feeder, the signal reflects on the glass that is situated on movable jaw and it goes back to the sensor. The machine stops feeding and waits for another bar.
- The roller conveyer goes through the whole machine and supports the material in all its length. The roller conveyer of the feeder: bearings houses of the rollers are mounted into the basement – big robustness and precision.
- The feeder (transporter) has it's own hydraulic unit.
- The feeder clamping vice is a robust steel weldment. Jaws ensure safe clamping of the material.
- Jaws of the feeding vice move along two-rails linears using hydric cylinder. One jaw is long stroke ( the movement by longstroke hydraulic cylinder). Second jaw is short stroke (utilization during bar feeding: not jaw wearing out, not slipping of material). Short stroke jaw is suitable for feeding of deformed material.
- The blade leading in guides with hardmetal plates and leading bearings and along cast iron pulleys.
- Machine is equipped with hydraulic system which controles all functions of that maschine. It pushes the arm to cut, pulls up the arm, opens and closes vices, moving of feeder.
- The blade is 8 grades sloped regarding the level of the vice => higher performance when cutting, profiles, longer bladelife, higher performance when cutting full materials.
- There is a guide situated on the firm beam on the drive side. On the tightening side there is the guide situated on the moving beam.
- The guide beams of moving band guide is adjustable in whole working range. Manual adjustment and fixing of the guide beams.
- Hydraulic tightening of band.
- Automatic indication of blade tension.
- A cleaning brush is driven by an electroengine and ensures perfect cleaning of a blade.
- There is a planet gear box drive and a three-phase electroengine, a fluent regulation of a blade speed by a frequency converter for a fluent change of blade speed.
- The cooling system for emulsion, leaded to the guides of the blade and by LocLine system directly to the cut groove.
- Massive base with a tank for chips. Base is designed for manipulation manipulation with machine by crane.
- Indication of blade tightening and opening of the cover.
- Controlling 24 V.
Basic equipment of machine:
- Lighting of workink space.
- Band saw blade.
- Set of spanners for common service.
- Manual instructions in eletronic form (CD).
Operating cycle:
After starting the machine, vices clamp after starting the machine, the machine makes the cut by a set speed, the cutting zone in the down position of the arm is released - the longstroke jaw of the firm vice open, the feeder moves the material to the firm vice, the arm lifts up to the set upper position. The material is moved by the feeder – periodic regime (feeder moves between zero position and the position of the set lenght of feed) or consecutive regime (feeder moves to the limit position and clamps the material and feed it to the cut consecutively). The main vice clamps the material, the vice of the feeder is still closed and the whole procedure repeats. The operator only loads the material and removes the cut material. It is possible to regulate the cutting speed of the arm and the blade speed during cutting.
Code | Description | Type | |
---|---|---|---|
SIEMENS HMI 7" | Controling system SIEMENS with display 7". | ST | |
PCP | One year subscription for external machine programming (for Siemens control system) using www server. | O | |
BLUEBOX | Router for remote saw service. | OP | |
CDC | Basic library with cutting parameters, operator inputs the material informations (dimensions, type, quality) Automatical setting of cutting parameters. Operator set only information about quality and dimension of material. | ST | |
ZAPSI | Industry 4.0, Connection to bandsaw monitoring and evaluation of machine efficiency, operation, production, and energy consumption. | OP | |
LED | Lighting of workink space. | ST | |
ECK | Cleaning brush of blade driven actively by motor. | ST | |
PEGAS ASR | ASR = Automatic cutting feed regulation based on set parameters. | ST | |
NPH | Hydraulic tension of band. | ST | |
RTS-A | Regulation press of vice – set of 2 pcs for bothvices. | ST | |
OCP | Rebounding jaw of feeder vice. Controled by short-stroke cylinder, placed on linear leading. | ST | |
1000-PUS | Prismatic clamps for cutting hexagonal tube bundles. Manual adjustment of the upper jaw for bundle size adjustment. This is a set of 1 clamp for fixed jaw and 1 clamp for movable jaw vice (for automatic saw you need to order 2pcs PUS). | OP | |
BOX-TRI-BIG | Box for the chips 200 l with emulsion draining to the waterproof tank. | O | |
1000-VTH | Chain chip extractor, includedd 1 pcs of BOX-TRI. | OP | |
1000-SRZ | Vice behind the cut. Hydraulic clamping of the material behind the cut. | OP | |
MINI LUBE 54 | Wasteless lubricating system – 2 pumps, for blade 54 mm. Instead of emulsion cooling, specially for cutting profiles and non-ferrous metals, necessary supply of pressed air 6 Atm. | O | |
LASER LINE | Laser indicator of cut position. | O | |
1000-ZO | The frame for transportation with the tarp. | ST | |
1000-HPR-A | Hydraulic upper clamping. Jaw clamps material in vertical direction using hydraulic cylinder and two axis of linear leading. Set of 2 pcs. | O | |
1000-SET M42 | Set of 10 blades in SPECTRA M42 quality – with customer’s choice of teeth. 8920x54x1,6 | O | |
1000-SET M51 | Set of 10 blades in DURATEC M51 quality – with customer’s choice of teeth. 8920x54x1,6 | O | |
1000-NAV | Manual instruction – printed version. | O | |
RDT 1000/1150 | Input or output robust roller conveyor with a gutter which prevents leakage of emulsion on the floor, it is possible to put them for RDP or RDZ. Lenght 1000 mm, width of cylinders 1150 mm, capacity 1700 kg/m. | O | |
RDT 2000/1150 | Robust roller conveyor with a gutter which prevents leakage of emulsion on the floor. Lenght 2000 mm, width of cylinders 1150 mm, 5 rollers, capacity 2000 kg/m. | O | |
SYNC-1 | Synchronisation of the saw feeder movement with the roller rotation of the RDM powered conveyor in the automatic cycle | OP | |
RDM 2000/1150 | Input or output robust roller conveyor with driven rollers . Driving by electrical engine, vorm gearbox and inverter. By chain are driving cylinders. Width of cylinders 1150 mm, length 2000 mm, capacity 2000kg/m. Impossibile use for automatical saws CNC !!! | OP | |
RDML 2000/1150 | Input or output robust roller conveyor with driven rollers. Driving from RDM throught chain. (RDM-L does not work without RDM conveyor) Width of cylinders 1150 mm, length 2000 mm. Load capacity 2000kg/m. | OP | |
1000-VZM | The roller table length 900 mm, width 1150 mm with 1 pc of pasive cylinder and one peace of driven cylinder. The roller which is driven by electroengine is able to lift the material hydraulically above the level of other rollers. It serves as the connecting part of the roller conveyors or for connecting of the roller conveyor and the machine. Control of the roller is independent on the controlling of the machine, the roller has its own controlling panel. | OP | |
RDH-1150 | Independent movable cylinder, adjustable height, capacity 1000kg. Width of roller 1150mm. | O | |
1000-RBR | Side support fixed cylinder, with its own frame, it is mounted to roller tables. | O | |
1000-RBRS | Side adjustable roller with its own steel frame, and with the movable leading. | O | |
1000-RBRS-H | Hydraulically movable side roller with it’s own frame. | OP | |
1000-RBRS INPUT | Side rollers mounted on a first input section of transporter. | O | |
RDT-XY1-1150 | Roller table setup (with one motorised 1000-VZM). The setup has total Length 7500 mm. In this option is included 4 powered cross-conveyors with Length of 4000 mm. The flow of material is one way, manual control. Max. weight of material transferred per one segment: 1000 kg.To increase efficiency. | O |
Tech. data NO241 are valid on 1.1.2024. Producer has the right to make changes of technical data.
Values contained on this page are only for information purposes. This information is not an offer and is not a public promise. This indicative offer does not give right to close a contract. The only guiding document for the contract is a valid price list.
or send inquiry!