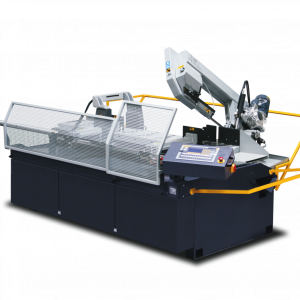
mm | 0° | 45° | 60° | -45° | -60° | ![]() |
![]() |
---|---|---|---|---|---|---|---|
![]() |
300 | 300 | 200 | 280 | x | x | x |
![]() |
180* | 110* | 80* | 110* | x | x | x |
![]() |
320x300 | 300x250 | 200x200 | 260x200 | x | 260x200 |
![]() |
![]() |
![]() |
![]() |
![]() |
---|---|---|---|---|
3x400V | 2,4 | 20-100 | 3660x27x0,9 | 1200 |
Lmin | Lmax | Bmin | Bmax | Hmin | Hmax | V |
---|---|---|---|---|---|---|
2547 | 2547 | 4632 | 4632 | 1560 | 2177 | 941 |
It is a highly efficient automatic hydraulically controlled band-saw with multiple material feed. The feeder of the material is combined with roller conveyor which suppports the material in the whole lenght ( 1500mm). The machine is designed for vertical and angular cuts. Angular cuts are fluently adjustable from 0 to +45 grades right in automatic mode and to +60° right in semiautomatic mode. It is suitable for serial production and thank to its robust construction enables to cut wide range of materials including stainless stells and tool steels both profiles and full materials.
Control systém:
Machine is equipped with programmable PLC SIEMENS SIMATIC S7-1200. Blade drive, bow movements and feeder movements are controled by SIEMENS technology.
The coloured touch screen HMI SIEMENS TP 700 COMFORT enables easy communication with an operator. It shows working conditions (blade speed, moving to the cut, cutting parameters etc.)
The machine enables to work with two modes:
SEMIAUTOMATIC CYCLE: The machine cuts the material immediatelly in a semiautomatic mode. The operator uses the feeder of the machine for the manipulation with the material and for the exact feed of the material into the cutting zone. The movement of the feeder is realized by manual buttons or by GTO function. After starting GTO function the operator sets the position of the feeder, presses START button and feeder goes to the set position.
AUTOMATIC CYCLE: the feeder feeds the material according to the set programm. The operator sets the cutting programm, machine realizes these programms, it is possible to make 200 different programms.The part of one programm is a complete setting of the cut: blade speed, feed speed, setting of an automatic regulation, setting of the hight of the bar to be cut, setting of the lenght of the bar, angles values and number of pieces. The lenght and number of pieces it is possible to set in 99 lines, the machine feeds differently set lenghts automatically. Control system shows the feasibility of the cutting by the drawings
Cutting feed rate is regulated by control system leaded by servomotor, ball screw and KM nut enabling very precise feed rate. The operator sets in the program needed feed rate (mm/min) and the machine will set it up. Two basic regimes of automatic system regulation (ASR): ARP a RZP-2.
RZP-2: cutting zones regulation. System enables to set of optimal shift speed (movement to cut) and blade speed in 5 different zones depending on blade position. An operator choose two ways of djustment: DEFENSIVE - suitable for cutting of very hard materials with carbide blades. The shift speed is slowed down on begining and ond end of cut. OFENSIVE - for productive cutting of solid round basrs. Shift speed and blade speed are raised on begining and end of the cut. It is a similar principle as ARP system. Anvantage is a possibility of blade speed regulation.
ARP = System of the automatic regulation of the cutting feed rate depending on the cutting resistance of the material or blunting the blade.
System offers two basic modes of ARP: BIMETAL and CARBIDE.
BIMETAL mode is suitable for optimalization of the cutting feed when cutting profiles by bimetal blades. The cutting feed is higher if the blade cuts sides of the profile. As the blade reaches the full material, the system reduces the cutting feed automatically so that teeth gap of the blade would not be filled.
CARBIDE mode is suitable for cutting of full bars. If the blade is old (blunt), loaded is the cutting feed reduced Reaction time is slower than in mode BIMETAL.
Safety module with autodiagnostics.
Construction:
The machine is constructionaly designed in that way, so that it corresponds to standard exertions in productive conditions. That is why all carrying parts are made as cast-iron castings (solidity, absorbtion of vibrations and stops). Parts of arm, vice and turn table is cust iron.
The arm of the machine is made of cust iron and it is designed to ensure the power and the precision of the cut. Arm is 30 grades sloped, it increases the lifetime of blade.
Arm is placed in adjustable bearings.
Drive pulley and tighten pulley are both metal castings.
Upper working arm position controled by automatic stopper (DPP)
The down working position of the arm controlled by the miscroswitch. In the end position microswitch is on, arm goes to selected upper position.
The vice is welded. The jaw is made from cast iron. Jaw ensures the safe clamping of the material.
The hydraulically operating vice with long travel is placed in an adjustable dovetail groove.
Moving jaw of the vice is handled by long stroke hydraulic cylinder.
Very massive feeder moves using hydraulic cylinder and two sparpened bars and teflon cases.
There is a floating seating of the feeding vice in the feeder, it means that the feeding vice moves in perpendicular sense regarding the feeding sense. The stationary jaw of the feeding vice copies the possible roughness of feeded material and the worning out of mechanical parts of the feeder is eliminated.
The feeder moves the material to be cut to the main vice according to the set lenght that was adjusted by the operator in the controlling panel. The position of the feeder is indicated by electromagnetic sensor and measuring magnetic tape. For a perfect placing of a feeder , feeder moves to end positions by a slow velocity.
Indication of material in the feeder: optic sensor - it notices that there is a material in the feeder. If there is no material in the feeder, the signal reflects on the glass that is situated on movable jaw and it goes back to the sensor. The machine stops feeding and waits for another bar.
The feeder clamping vice is made from cast iron. Jaws ensure safe clamping of the material.
Hydraulic, long stroke cylinder of the feeder is placed in adjustabled dovetail groof. Moving jaw of the vice is handled by long stroke hydraulic cylinder.
A turntable is massive welded. A turntable gives a big place for supportion of material and its perfect clamping.
Manuall turning of the table for angle cuts, angle fixation using quick clamping lever.
The angles indicated on the digital display show the turning of the turntable. Reading of angle by incremental sensor and magnetic tape.
Basic equipment of machine:
The blade leading in guides with hardmetal plates and leading bearings and along cast iron pulleys.
There is a guide situated on the firm beam on the drive side. On the tightening side there is the guide situated on the moving beam.
The guide beams of moving band guide is adjustable in whole working range. Manual adjustment and fixing of the guide beams.
Guide holder moves in adjustabled dovetail groof.
The saw-band is equipped with a guard, which protects the operator from millings and cutting emulsion.
Mechanic tightening of the blade.
Automatic indication of blade tension.
A passive driven cleaning brush for perfect cleaning and function of blade.
Drive of machine is solved by worm gear box with maintenanceless oil filling. Three-phases electromotor with double winding, with a frequency converter for a fluent regulation of the blade speed from 20 to 100 m/min. Sturdy flange with shaft. Termoprotection of engine.
Cooling system for emulsion with liquid distribution to blade guides. Nádrž na emulzi je samostatná sestava, není pevnou součástí podstavce.
Massive base with a tank for chips. Base is designed for manipulation manipulation with machine by pallet truck and also by any hight lift truck.
Indication of blade tightening and opening of the cover.
Controlling 24 V.
Machine is equipped with hydraulic system which controles all functions of that maschine. It pushes the arm to cut, pulls up the arm, opens and closes vices, moving of feeder.
Basic equipment of machine:
Slide of cut pieces.
Band saw blade.
Set of spanners for common service.
Manual instructions in eletronic form (CD).
Operating cycle:
The machine automatically grips the material in the main vice and the feeder moves into a position determined by the processor (i.e. the required length of the cut and a constant added length); the feeder-vice’s jaw stays open. The arm moves into the cut; after cutting the material, it moves into the upper position. The feeder moves by the constant added length (exactly to a position determined by the processor) and the feeder jaw grips the material. The vice is released; the feeder moves the material into the zero position (by the required length). The main vice grips, the feeder-vice is released and the entire cycle is repeated.The operator only removes the sawn material.
Code | Description | Type |
---|
Tech. data NO241 are valid on 1.1.2024. Producer has the right to make changes of technical data.
Values contained on this page are only for information purposes. This information is not an offer and is not a public promise. This indicative offer does not give right to close a contract. The only guiding document for the contract is a valid price list.